Why CMMS Is Vital In Construction Projects
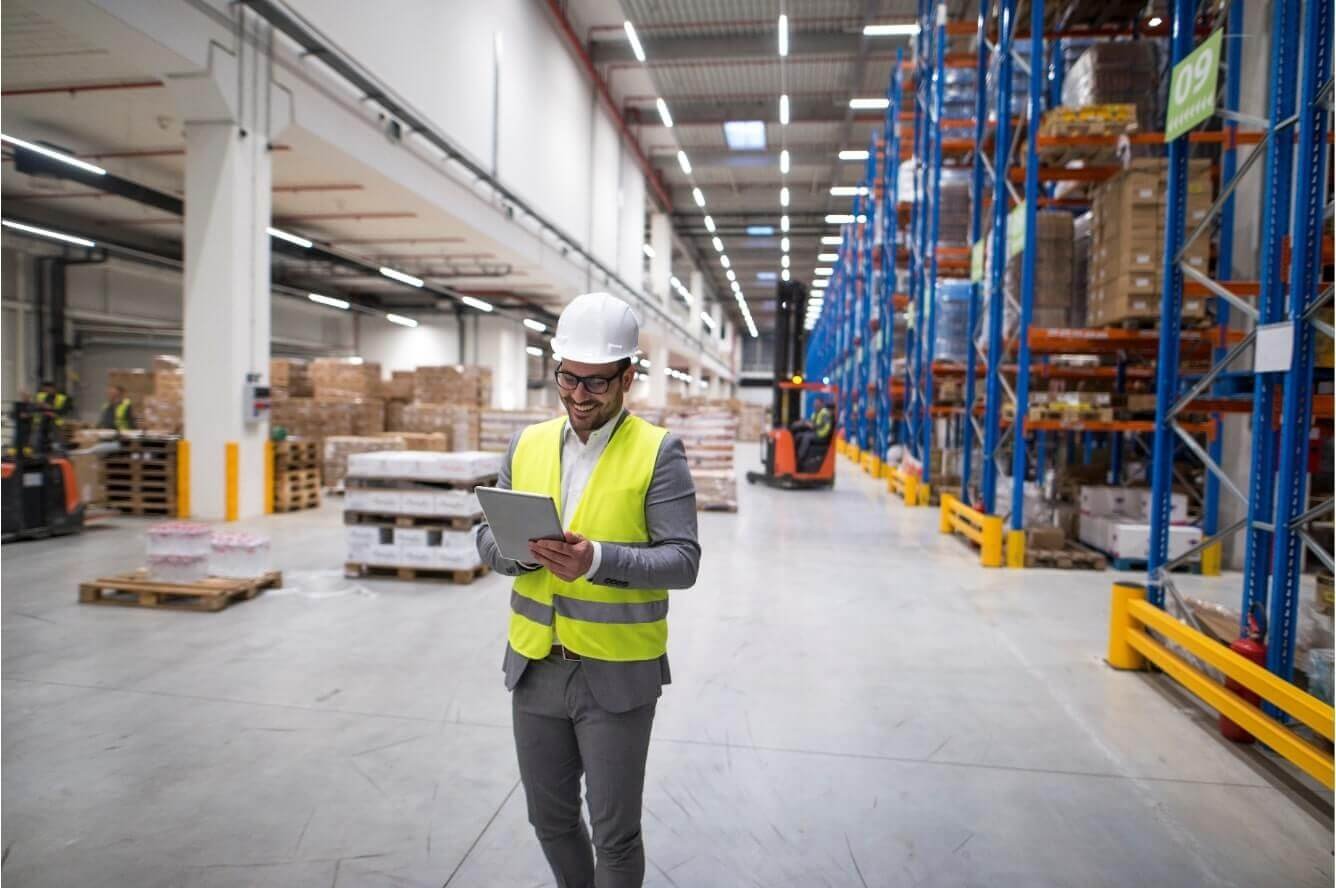
You may wonder why a CMMS is so crucial to the construction industry. A CMMS is an application that helps manage the maintenance of equipment on construction projects. It is particularly useful for construction companies with key indicators. Some examples of these key indicators are: Work order management, Condition monitoring sensors, and access to data. If you’re looking to streamline maintenance tasks, consider a CMMS geared to the construction industry.
Work order management
There are many reasons to use work order management in construction projects. First, work orders can be customized to meet the needs of each project. For example, a maintenance department can be expected to complete 50 repairs per day, while the actual number of repairs may be only forty-five. Then, work orders can be broken down into smaller tasks. This can make it much easier for team members to execute a task. Furthermore, work order management can be modified over time as the project grows and changes.
Another benefit is that work order management software can track asset resources. These assets can include warranty information, regulatory expectations, maintenance records, and depreciation data. In addition, work order management software features reporting capabilities that can help project managers analyze the status of projects. The software also provides information about predictive maintenance, future needs, and optimal preventive maintenance schedules. If you’re looking for work order management software, check out these five reasons to get the most out of it.
A construction project can be a real headache if a team doesn’t keep track of its work orders. If communication isn’t effective, the project could get delayed. A cloud-based document management software can solve this problem. With real-time data, it helps users organize projects in a central location. Kanban boards help team members manage work orders by adding attachments and defining priorities. Work orders are then placed under columns that reflect the phases of a project.
A work order can be scheduled for a specific date, scheduled maintenance triggers, or dedicated blocks of time. Having a deadline for each work order ensures that employees are held accountable for the work orders. The documentation also supports safety audits. Lastly, work order management provides a framework for documenting the status of maintenance procedures. If a work order doesn’t reach its deadline, it won’t be completed.
Cloud-based CMMS software
Modern CMMS software is often cloud-based, which means that it is not installed on site. Users simply log on to their cloud-based CMMS system and access the data from anywhere. Cloud-based CMMS systems are usually highly available, with over 98% uptime, so they can be used anywhere. And, because they are web-based, they are always available no matter where they are.
One of the main benefits of using a cloud-based construction management system is security. Unlike software that is stored on a company’s own servers, cloud-based tools are secured by service providers and follow strict security guidelines. This means that even if someone steals your laptop or smartphone, you’re less likely to worry about losing important information. Another advantage of cloud-based construction management software is its ability to be used from other devices. Moreover, because it is often paid for, cloud-based construction management systems are a highly cost-effective option.
Before selecting a CMMS system, facility owners should consider their needs and goals. A good solution should also be scalable and allow for future growth. A small organization will need a simple software solution, while a growing organization will need something more sophisticated. A large company with several locations and multiple buildings will likely need a more sophisticated solution that can expand as the organization grows. Therefore, it’s important to consider the size of the construction project and choose the right CMMS solution.
In addition to providing project management capabilities, cloud-based CMMS software helps construction businesses improve their processes and increase the efficiency of existing employees. BIM (Building Information Modeling) software enables construction teams to collaborate on building designs. By collaborating on building designs with the software, teams can view 2D and 3D models. They can then communicate with each other and avoid costly design errors. That reduces the risk of costly mistakes that can arise in the future.
Integration with condition-monitoring sensors
While sensor-based technologies are a hot topic, integration with construction projects is still an underexplored field. Despite its potential, little is known about the practical applications of these technologies. As a result, we sought to conduct an in-depth investigation and a systematic review of the literature. In this way, we were able to uncover the potential benefits of condition-monitoring sensors for construction projects.
This type of monitoring system consists of three major functional subsystems: the Data Acquisition Unit (DAU), Alarm Module, and System Controller. All three of these components have redundant data buses that allow for automatic transfer in the event of a system failure. Because the operating system is designed to maintain protection even when the links to the System Controller fail, once programmed, they must continue to function to provide safety.
Despite these challenges, the benefits of condition-monitoring technologies are clear. With better integration of condition-monitoring sensors, construction managers can improve the performance of their projects. Monitoring systems can detect structural rotation, cracking, and differential movement. These sensors can even measure building vibration. And with the ability to monitor a range of parameters, continuous maintenance monitoring can improve the performance of construction projects.
One way to improve construction safety management is to integrate sensors and WSNs. Sensor-based technologies are becoming more sophisticated and popular as construction projects increase in complexity. A balance of software and hardware is necessary to facilitate its use. Smartphones have proven to be an excellent platform for sensor-based technologies. They can incorporate a variety of sensor-based technologies and have a low manufacturing cost. It makes them more affordable to manufacture, resulting in more widespread usage and wider benefits.
Accessibility
A CMMS for accessibility in construction projects is a great tool for organizations that need to track and manage accessibility issues in their construction projects. It allows maintenance staff to capture images of bar coded equipment for easy identification. By integrating CMMS software applications with mobile devices, maintenance staff can identify equipment in need of repair. By scanning equipment bar codes, a CMMS reduces delays and the chance of mistakes. Maintenance staff can no longer search for equipment parts by serial number, which can cause unintended errors. Bar code scanning allows maintenance staff to order and track parts in one step, without having to waste valuable time searching for them.
CMMS for accessibility in construction projects can help organizations manage their inventory, improve productivity, and streamline workflow. It can manage work orders and service requests from anywhere, and it can even be accessed through a mobile device. This allows employees to easily access the system and perform maintenance tasks from anywhere. This is important in an increasingly mobile world. In addition to its ability to track inventory, a CMMS for accessibility in construction projects can also help organizations manage inventory levels and notify employers when more stock is needed. Using a CMMS for accessibility in construction projects allows companies to create in-depth reports that provide valuable insight into the status of a construction project.
Another great benefit of a CMMS for accessibility in construction projects is that it can manage multiple vendors and projects. By using a mobile-compatible CMMS, employees can easily issue work orders, monitor progress, and track costs. Besides the ability to manage multiple vendors, CMMS systems can track inventory and manage maintenance schedules, as well as assign inventory. This means CMMS software for accessibility in construction projects is crucial for any type of construction business.
Cost
Implementing CMMS software has many advantages. It makes work orders easier to process, improves regulatory compliance, and reduces occupant complaints. It can also be used to manage several vendors and track costs. This software can make it easy for you to issue work orders to contractors. And with a refresher course, you can see how valuable the data it stores can be for your construction project. Learn how to use a CMMS to improve your bottom line.
The initial investment for a CMMS solution can be as low as $15,000 for a typical facility. This price includes all software and setup, plus basic training. Some solutions can cost even more, depending on the number of users and the type of software. However, you can measure how much it improves productivity by comparing the costs of using a CMMS to the cost of the same services or products from other companies.
Preventative maintenance helps you avoid costly emergency repairs. These costly repairs take time and require technicians to be pulled from other jobs. You may also have to pay premium shipping costs to get the parts you need quickly. If inventory issues occur, production lines may stop and workers must miss work. Miscommunication and oversights can also cost you money. CMMS systems can address these issues in a single software package. If you’re unsure about the cost of CMMS software, check out the benefits that it can offer your construction project.
A CMMS system may include a module that stores detailed records of equipment. This module can store equipment-related data such as a bill of materials, PM schedule, and service contracts. It also keeps track of safety procedures and measurement points. In addition, CMMS can track maintenance requests. This way, you’ll know when it’s time for a maintenance task. You can then make informed decisions about how much you should spend on that specific component.